Key Advantages and Factors To Consider of Implementing Plastic Extrusion in Your Tasks

Recognizing the Fundamentals of Plastic Extrusion
Plastic extrusion, a staple in the production market, is a procedure that involves melting raw plastic product and reshaping it right into a continuous profile. This account, when cooled, can be reduced right into desired sizes or coiled for later use. The beauty of plastic extrusion hinges on its versatility. A wide variety of products, from piping to window frameworks, can be generated. The process requires an extruder, an elaborate maker with a heated barrel, a rotating screw, and a die at the end. The plastic product, in the form of pellets, is fed into the extruder, where it's melted and forced with the die, taking its shape. The option of plastic and the design of the die establish the product's characteristics.

The Economic Advantage of Plastic Extrusion
The financial benefit of plastic extrusion lies primarily in two locations: economical product manufacturing and advantageous manufacturing rates. With plastic extrusion, companies can create high quantities of product at a lower price compared to other methods. The process flaunts an impressive production speed, substantially minimizing time and more boosting its financial practicality.
Affordable Material Production
A substantial benefit of plastic extrusion is its remarkable cost-effectiveness. This manufacturing procedure permits continuous, high-volume production with minimal waste, which equates right into lower prices. The raw materials used, normally plastic pellets, are reasonably inexpensive contrasted to other compounds (plastic extrusion). The procedure itself calls for less power than lots of various other manufacturing approaches, better decreasing expenses. Additionally, the extrusion process enables a high level of precision in shaping the plastic, lowering the need for expensive post-production changes or modifications. In addition, the toughness and longevity of extruded plastic products frequently suggest less require for replacements, adding to lasting financial savings. All these elements make plastic extrusion a highly cost-effective selection for several tasks, using an appealing equilibrium between price and efficiency.
Beneficial Manufacturing Speeds
While maintaining the cost-effectiveness of the materials, another notable benefit of plastic extrusion depends on its quick production rates. This efficiency in the production process is credited to the continuous nature of the extrusion procedure, enabling high-volume production in a fairly brief time period. The speed of manufacturing directly associates to a decline in labor expenses and a boost in output, thus improving the general financial feasibility of the process. The fast-paced manufacturing does not compromise the high quality of the final product, making sure dependable and regular results. This combination of rate, cost-effectiveness, and quality underscores the significant economic advantage of applying plastic extrusion in various projects.
Convenience and Customization: The Staminas of Plastic Extrusion
One of the noticeable staminas of plastic extrusion depends on its convenience and personalization potential. These top qualities open go to my site up the door to endless layout opportunities, providing makers the capability to tailor products to particular needs. This heightened level of personalization not only improves item capability yet also dramatically improves product originality.
Endless Layout Possibilities
Plastic extrusion shines in its ability to offer nearly limitless layout opportunities. This method supplies liberty to create complex forms and detailed profiles, an accomplishment tough to achieve with various other fabrication strategies. Owing to the fluid nature of liquified plastic, the process is adaptable enough to yield a diverse variety of dimensions, dimensions, and forms. The plastic can be controlled to match distinct specifications, enabling for the manufacturing of personalized geometries and conference certain client needs. Plastic extrusion can deal with a selection of plastic types, increasing its application range. This versatile technique, consequently, serves a variety of industries from building and construction to vehicle, packaging to electronic devices, and beyond. With plastic extrusion, the design possibilities are basically unlimited.
Improving Item Uniqueness
The adaptability of plastic extrusion can significantly boost product individuality. This procedure permits developers to experiment with various forms, sizes, and shades, providing them the liberty to create unique items that go to my site attract attention in the marketplace. It is this modification that offers an unique identification per item, differentiating it from its competitors.
Along with its visual advantages, the customizability of plastic extrusion also supplies functional benefits. Designers can change the residential properties of the plastic according to the certain requirements of the application, enhancing the item's performance. As an example, they can make the plastic more flexible, extra durable, or much more resistant to warmth, relying on what the item calls for. Thus, plastic extrusion not just increases product originality yet also its energy and marketability.
Design Limitations in Plastic Extrusion: What You Need to Know
Just how can design limitations potentially impact the procedure of plastic extrusion? While plastic extrusion is functional, layout constraints can reduce its benefits. Recognizing these restraints is crucial for reliable implementation of plastic extrusion in your projects.
Assessing the Environmental Impact of Plastic Extrusion
While understanding design limitations is a significant aspect of plastic extrusion, it is just as vital to consider its ecological effects. The procedure of plastic extrusion entails melting plastic products, possibly releasing dangerous gases right into the environment. Further, the resulting products are usually non-biodegradable, adding to land fill waste. Innovations in technology have permitted for even more environmentally-friendly practices. For circumstances, using recycled plastic products in the extrusion process can decrease ecological effect. In addition, establishing eco-friendly plastic options can help reduce waste problems. Assessing these ecological variables is crucial when executing plastic extrusion jobs, making certain an equilibrium between performance, cost-effectiveness, and ecological duty.
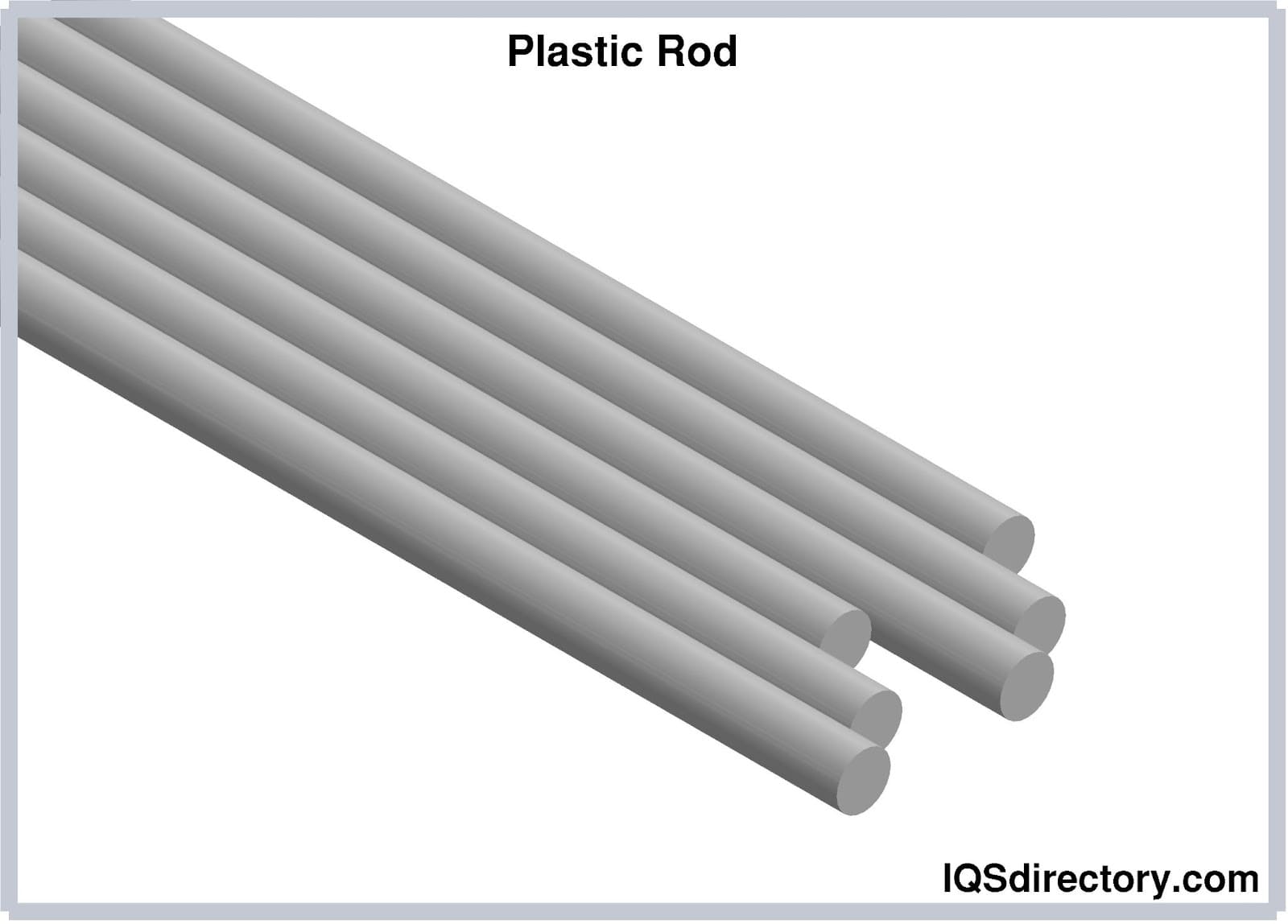
Instance Research: Successful Projects Utilizing Plastic Extrusion
Success stories in the field of plastic extrusion are plentiful, demonstrating both the adaptability and effectiveness of this production procedure. plastic extrusion. An additional successful case is the manufacturing of plastic movie for product packaging and agriculture. These instances illustrate plastic extrusion's essential function in various markets, testifying to its adaptability, cost-effectiveness, and trusted outcome.
Conclusion
In final thought, plastic extrusion offers a cost-effective and reliable technique for generating complex forms with marginal waste. Incorporating plastic extrusion into jobs can lead to effective outcomes, as confirmed by numerous situation studies.
Plastic extrusion, a staple in the production sector, is a process that entails melting raw plastic product and he said reshaping it right into a continual account. Plastic extrusion can handle a selection of plastic kinds, broadening its application scope.Just how can make constraints possibly impact the procedure of plastic extrusion? The process of plastic extrusion involves melting plastic materials, possibly releasing unsafe gases right into the atmosphere. Utilizing recycled plastic materials in the extrusion procedure can minimize ecological effect.
Comments on “Plastic extrusion used in building, automotive, and more”